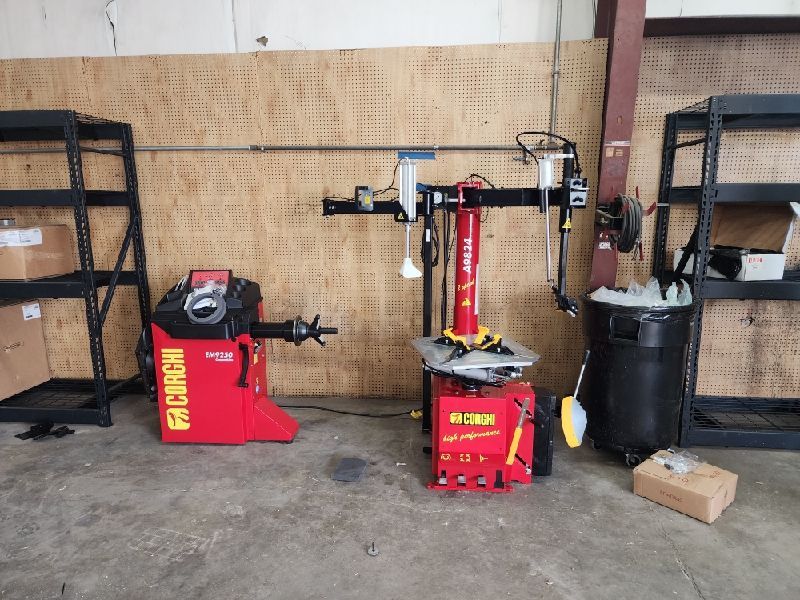
Maximize the Lifespan of Your Tire Machines with These Expert Maintenance Tips
Tire machines are a big investment, and proper maintenance keeps them running longer and performing better. Every time you mount or balance a tire, the machine takes on stress. Neglecting maintenance leads to breakdowns, costly repairs, and lost productivity.
A well-maintained tire machine works faster, smoother, and more accurately. When parts wear out or build-up slows operations, technicians struggle to get the job done right. That means longer service times, frustrated employees, and unhappy customers.
The good news? A few simple maintenance steps can extend your machine’s lifespan and keep your shop running efficiently. This guide breaks down everything you need to know to prevent breakdowns, improve performance, and protect your investment.
Follow a Regular Cleaning and Maintenance Schedule
Keeping your tire machines clean and well-maintained prevents buildup, reduces wear, and ensures smooth operation. Dirt, grease, and debris can clog moving parts, causing friction and premature failure. A consistent maintenance schedule keeps everything running like new.
Wipe Down and Clean After Every Use
Tire machines deal with rubber shavings, lubricants, and dirt all day. Leaving residue on the machine can cause buildup and affect performance. After each use:
- Wipe down all surfaces with a clean cloth to remove dirt and grease.
- Use a mild degreaser to clean key components like clamps, mounting heads, and turntables.
- Check for leftover tire lube or debris that could cause slippage or inaccurate mounting.
Inspect for Wear and Damage Weekly
A quick weekly inspection can catch small problems before they turn into costly repairs. Check:
- Hoses and seals for cracks or leaks.
- Clamps and moving parts for wear or rust.
- Cables and electrical connections for loose wires or exposed insulation.
- Turntable and bead breaker for smooth movement and proper alignment.
Deep Clean and Lubricate Monthly
At least once a month, take extra time to deep clean and lubricate essential components:
- Remove built-up grease and dirt from hard-to-reach areas.
- Lubricate moving parts like the turntable, bead breaker, and pedal assemblies.
- Check calibration and make adjustments if needed.
Regular cleaning and maintenance keep your tire machines running smoothly, efficiently, and for years to come.
Properly Lubricate Moving Parts
Lubrication is one of the easiest ways to extend the life of your tire machines. Without it, friction causes parts to wear out faster, leading to breakdowns and expensive repairs. A well-lubricated machine runs smoothly, reduces strain on components, and improves overall performance.
Know Which Parts Need Lubrication
Not all parts of a tire machine need lubrication, but some require it regularly to prevent wear. Focus on:
- Turntable and Clamps – Ensures smooth tire mounting and prevents sticking.
- Bead Breaker Arm – Reduces resistance when breaking a tire bead.
- Pedal Assemblies – Keeps foot controls responsive and easy to use.
- Air Cylinders and Pivot Points – Prevents rust and stiffness in moving parts.
Use the Right Lubricant
Using the wrong lubricant can do more harm than good. Stick with:
- White lithium grease for metal-on-metal components.
- Silicone-based lubricants for rubber seals and O-rings.
- Light machine oil for pivot points and small moving parts.
Avoid using
WD-40 or generic spray lubricants on high-wear parts. They evaporate quickly and don’t provide lasting protection.
Lubricate on a Set Schedule
How often you lubricate depends on how much you use the machine, but a good rule of thumb is:
- Daily for high-use shops – A quick application on essential parts.
- Weekly for moderate use – A full lubrication check-up.
- Monthly deep lubrication – Clean old grease and reapply fresh lubricant.
Skipping lubrication leads to stiff movement, noisy operation, and premature part failure. A few minutes of maintenance keeps everything running smoothly and prevents costly downtime.
Calibrate and Adjust for Precision
Even the best tire machines lose accuracy over time. Misalignment leads to uneven wear, poor tire mounting, and costly mistakes. Regular calibration keeps your machine working at peak performance and prevents unnecessary strain on components.
Check Alignment Before Every Shift
A quick alignment check at the start of each workday ensures accuracy and prevents errors. Before using the machine:
- Inspect the turntable – Make sure it’s level and rotates smoothly.
- Check bead breaker alignment – It should contact the tire sidewall evenly.
- Test clamp positioning – Clamps should grip the wheel securely without excessive force.
If something feels off,
adjust it before starting work. A minor misalignment can lead to
damaged tires, scratched rims, or machine breakdowns.
Recalibrate Sensors and Gauges Monthly
Tire machines with built-in air pressure gauges, bead seating controls, or automated settings need regular recalibration to stay accurate. Every month:
- Compare pressure readings with a manual gauge – If there's a difference, adjust the machine.
- Check the bead seater's inflation speed – It should provide a controlled burst, not inconsistent airflow.
- Recalibrate digital displays – If your machine has an electronic interface, follow the manufacturer’s calibration process.
Tighten and Adjust Moving Parts as Needed
Loose components affect accuracy and efficiency. Inspect and tighten:
- Bolts and fasteners – Prevents unnecessary vibrations and instability.
- Clamps and turntable arms – Ensures a secure grip on the wheel.
- Bead breaker cylinder – Keeps movement smooth and effective.
A properly calibrated tire machine reduces errors, prevents uneven wear, and extends the machine’s lifespan. Regular adjustments keep operations smooth, safe, and efficient.
Inspect Hydraulic and Pneumatic Systems
Hydraulic and pneumatic systems power key functions of your tire machines, including bead breaking, inflation, and clamping. Leaks, pressure loss, or worn-out components can cause weak performance, slow operation, and even machine failure. Regular inspections prevent costly breakdowns and keep everything running at full capacity.
Check for Air and Hydraulic Leaks Weekly
Leaks reduce system efficiency and lead to inconsistent pressure and weak operation. Every week, inspect:
- Hoses and fittings – Look for cracks, wear, or loose connections.
- Hydraulic cylinders – Watch for oil drips or slow movement.
- Air compressor connections – Ensure fittings are secure and there’s no pressure drop.
If you notice hissing sounds, visible oil leaks, or weaker operation, fix the issue immediately. Small leaks quickly turn into major failures.
Monitor Air Pressure and Fluid Levels
Inconsistent pressure affects clamping force, bead breaking, and inflation accuracy. Keep an eye on:
- Air pressure gauges – Make sure they match the recommended PSI.
- Hydraulic fluid levels – Low levels cause sluggish movement and potential damage.
- Moisture in air lines – Drain the air compressor regularly to prevent water buildup.
Replace Worn-Out Seals and Filters
Old seals, gaskets, and filters weaken the system and reduce efficiency. Every few months:
- Replace worn-out rubber seals to prevent leaks.
- Swap out clogged air filters to maintain airflow.
- Check hydraulic fluid quality and replace it if it looks dirty or contaminated.
Hydraulic and pneumatic systems keep your tire machine running smoothly. Regular inspections prevent pressure loss, extend machine life, and ensure powerful performance.
Use the Right Accessories and Tools
Using the wrong accessories can damage your tire machine and shorten its lifespan. Cheap or incompatible tools cause excessive wear, misalignment, and even costly breakdowns. Sticking to the right equipment ensures smooth operation, better performance, and longer machine life.
Choose High-Quality Mounting and Demounting Tools
Mounting and demounting tires put a lot of pressure on the machine’s moving parts. Using low-quality or worn-out tools can scratch wheels, damage tires, or stress machine components. Always use:
- Properly sized mounting heads – Avoid universal or ill-fitting heads that can cause slipping.
- Durable nylon inserts – Protect rims from scratches during tire changes.
- Premium tire irons and levers – Cheap tools bend easily and put extra strain on the machine.
Match Clamps and Adapters to Wheel Types
Not all wheels fit securely with standard clamps. Using the wrong clamps or adapters leads to improper mounting and potential machine damage. Choose:
- Plastic clamps for alloy wheels – Prevents scratching and damage.
- Adjustable adapters for large tires – Ensures proper grip on oversized wheels.
- Low-profile attachments for performance tires – Prevents pinching or uneven pressure.
Invest in Quality Air Hoses and Fittings
Weak or damaged air hoses reduce inflation efficiency and cause pressure inconsistencies. Always use:
- Heavy-duty, reinforced air hoses – Prevents cracking and leaks.
- Quick-connect fittings – Ensures a secure, airtight seal.
- Correct PSI-rated accessories – Avoids strain on the air system.
Cheap accessories may save money upfront, but they cost more in repairs and lost productivity. Investing in the right tools keeps your tire machine working efficiently and extends its lifespan.
Train Employees on Proper Handling
Even the best tire machines won’t last if they’re handled poorly. Incorrect use leads to unnecessary strain, damaged components, and costly repairs. Proper training ensures your team knows how to operate the machine correctly, reducing wear and maximizing its lifespan.
Teach the Basics of Safe Operation
Every technician should understand how to operate the machine without causing damage. Cover:
- Correct tire mounting and demounting techniques – Avoid forcing the tire onto the rim, which strains the turntable and mounting head.
- Proper use of clamps and bead breakers – Misuse can lead to excessive pressure, damaging machine components.
- How to adjust air pressure settings – Overinflating or underinflating affects both tire safety and machine longevity.
Emphasize Preventing Common Mistakes
Many machine failures come from avoidable mistakes. Train employees to:
- Never force a stuck tire – If a tire won’t mount or demount smoothly, check for alignment issues instead of applying more pressure.
- Use the right settings for different tire sizes – Incorrect settings wear out moving parts faster.
- Avoid excessive lubrication – Too much tire lube makes the tire slip and reduces machine grip.
Schedule Refresher Training Sessions
Even experienced technicians develop bad habits over time. Hold regular training sessions to:
- Review best practices and reinforce proper techniques.
- Introduce new features or updates if the shop upgrades equipment.
- Address common issues and mistakes seen in daily operations.
A well-trained team extends the lifespan of your tire machines by using them correctly and preventing unnecessary wear. Investing in training saves money in repairs and keeps operations running smoothly.
Store Equipment in a Controlled Environment
Where you store your tire machines
affects their lifespan just as much as how you use them. Exposure to
dust, moisture, and extreme temperatures can cause premature wear, rust, and electrical issues.
Proper storage keeps your machines in top condition and prevents unnecessary repairs.
Protect Against Temperature and Humidity Damage
Tire machines contain metal, rubber, and electronic components—all of which react to temperature changes. To avoid damage:
- Keep machines in a temperature-controlled space – Extreme heat can dry out lubricants, while freezing temperatures can cause hydraulic fluid to thicken.
- Use dehumidifiers in humid areas – Excess moisture leads to rust, corrosion, and electrical malfunctions.
- Avoid placing machines near exterior doors or vents – Direct exposure to outside air causes condensation buildup.
Keep the Area Clean and Free of Debris
Dust, dirt, and small debris can clog moving parts and affect performance. Maintain a clean workspace by:
- Sweeping and wiping down surfaces daily – Prevents buildup in key components.
- Keeping machines away from welding or grinding stations – Metal shavings and sparks can cause serious damage.
- Using protective covers when machines aren’t in use – Shields against dust and accidental spills.
Ensure Proper Electrical and Air Supply Safety
Improper storage can lead to power surges, pressure drops, or air leaks. To prevent issues:
- Check power outlets and connections regularly – Loose or faulty wiring can cause short circuits.
- Ensure air compressors are in a dry, ventilated space – Excess moisture in the lines affects machine performance.
- Store air hoses properly – Prevents cracks and kinks that reduce airflow efficiency.
A controlled storage environment reduces wear, prevents costly repairs, and keeps your tire machines running at peak performance for years.
Schedule Preventative Maintenance Checks
Routine maintenance isn’t just about fixing problems—it’s about preventing them before they happen. A structured maintenance schedule extends the life of your tire machines, reduces downtime, and saves money on costly repairs.
Follow a Maintenance Checklist
Sticking to a set schedule keeps your tire machines running at peak performance. Use this breakdown:
- Daily – Wipe down surfaces, check for debris, and inspect clamps for proper function.
- Weekly – Inspect hoses, seals, and air pressure levels. Tighten any loose bolts.
- Monthly – Lubricate moving parts, check calibration, and clean hard-to-reach areas.
- Every 6 months – Deep clean the entire machine, replace worn-out seals, and check hydraulic/pneumatic systems.
Schedule Professional Inspections
Even with regular maintenance, some issues require a trained technician. Every year, have a professional inspect:
- Hydraulic and pneumatic systems – Ensure pressure levels are stable and components are leak-free.
- Electrical components – Check for wiring damage, loose connections, or motor wear.
- Structural integrity – Look for hidden cracks, rust, or wear on the frame.
Log All Maintenance and Repairs
Keeping maintenance records helps track wear patterns and prevent unexpected breakdowns. Log:
- What was cleaned, lubricated, or replaced
- Any performance issues noticed
- Dates of professional inspections and repairs
A structured maintenance plan keeps your tire machines in top shape, ensuring they last for years while operating smoothly. Preventative care costs less than emergency repairs—so stay ahead of issues before they turn into big problems.
Conclusion
Taking care of your tire machines isn’t just about keeping them running—it’s about protecting your investment, improving efficiency, and preventing costly downtime. Regular cleaning, proper lubrication, accurate calibration, and professional maintenance extend the lifespan of your equipment and keep your shop operating smoothly. By following these simple maintenance steps, you’ll get the most out of your tire machines while avoiding unnecessary repairs and replacements.
If you're looking for high-quality tire service equipment, automotive lifts, or compressed air systems, L & D Shop Solutions has you covered. They provide top-tier automotive equipment for both homeowners and auto shops, specializing in Rotary automotive lifts, Corghi and Rotary tire service equipment, and Eaton air compressors—all known for their reliability and performance. Based in Angier, NC, Holly Springs, and Apex, L & D Shop Solutions goes beyond just selling products—they offer turnkey solutions, expert installation, and a personal one-year warranty for added peace of mind.
Upgrade your shop with durable, high-performing equipment backed by top-notch service and industry expertise. Visit L & D Shop Solutions today to get started!