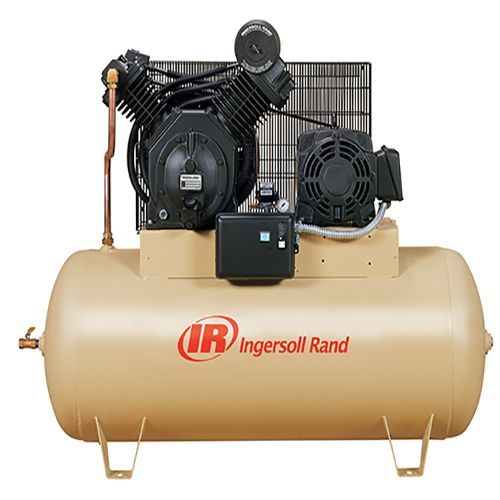
Signs That You Needs Repairs or Replacement For Your Air Compressor
Air compressors power the tools and equipment that keep your automotive shop running smoothly. When they start acting up, your workflow can grind to a halt. These issues don’t just slow you down—they can also cost you time, money, and even customers.
By spotting the warning signs early, you can avoid costly repairs and keep your shop running at full speed. In this blog, we’ll cover the common problems air compressors face, how they affect your business, and when you should think about repairs or replacement.
Need professional air compressor services? Check out our guide to expert solutions here.
Why Air Compressors Are Essential for Automotive Businesses
Air compressors are the workhorses of any automotive shop. Without them, many day-to-day tasks would be impossible to complete efficiently. They provide the power needed to run tools and equipment, making them a critical part of your shop’s operations.
What Air Compressors Do in Automotive Shops
- Power Pneumatic Tools
Air compressors are the driving force behind tools like impact wrenches, air ratchets, and grinders. Without consistent air pressure, these tools can’t perform reliably. - Support Tire Inflation
Whether you’re inflating a standard car tire or a larger commercial vehicle tire, an air compressor ensures the job gets done quickly and accurately. - Enable Spray Painting Applications
From touch-ups to full paint jobs, air compressors are essential for achieving smooth and even finishes.
How a Faulty Compressor Impacts Your Shop
A failing air compressor doesn’t just slow things down—it can completely disrupt your operations. Imagine losing power to your tools during a busy day or delivering subpar work because of inconsistent performance. When your equipment isn’t reliable, it affects everything from worker productivity to customer satisfaction.
Common Issues Indicating Repairs Are Needed
Recognizing the warning signs of a failing air compressor can save you from costly downtime and repairs. Here are the most common issues to watch for:
Inconsistent Air Pressure
If your tools aren’t performing at their best, your air compressor might be delivering uneven pressure. This can make tasks like tightening bolts or inflating tires more difficult and less precise. Fluctuating air pressure often points to worn-out seals, a failing pressure regulator, or internal leaks.
Unusual Noises
Air compressors should operate smoothly. If you hear hissing, banging, or clicking noises, something’s wrong. These sounds could mean:
- Loose or damaged internal components.
- Problems with the motor or bearings.
- Air leaks in the system.
Ignoring these noises can lead to bigger, more expensive problems.
Excessive Moisture
Finding water or oil in your compressed air is a clear red flag. This happens when the compressor’s moisture control system fails. Moisture contamination can:
- Damage your tools.
- Lower the quality of your work (especially in paint applications).
- Corrode the compressor over time.
Overheating
Overheating is a serious issue. If your air compressor is shutting down frequently or feels excessively hot to the touch, it’s struggling to keep up. Common causes include:
- Dirty air filters restricting airflow.
- A failing cooling system.
- Overworking the compressor beyond its capacity.
Increased Energy Consumption
A compressor working harder than it should will show up on your energy bills. If you notice higher utility costs, it might be due to inefficient operation caused by worn-out parts or air leaks.
Oil Leaks
If you spot oil pooling under the compressor, it’s time to call for repairs. Oil leaks not only affect performance but can also lead to safety hazards and more significant mechanical issues.
Frequent Motor Cycling
When your compressor starts and stops more frequently than normal, it’s a sign of trouble. Known as short cycling, this problem can stem from:
- A clogged intake filter.
- A faulty pressure switch.
- Leaks in the system.
When to Consider Replacing Your Air Compressor
Repairs can often extend the life of your air compressor, but there comes a time when replacement is the smarter choice. Knowing when to replace your equipment can save you from constant breakdowns, rising repair costs, and lost productivity.
Age of the Compressor
Most air compressors have a lifespan of 10–15 years, depending on the quality and maintenance. If your compressor is approaching or exceeding this range, it’s likely not operating as efficiently as it once did. Older compressors also tend to consume more energy, adding unnecessary costs to your shop.
Frequent Breakdowns
If you’re calling for repairs every few months, it’s time to weigh the costs. Frequent repairs add up quickly, and downtime can cost you customers. When the cost of fixing your compressor exceeds its value, replacing it is the better option.
Unable to Meet Demand
As your shop grows, so do your air compressor needs. If your current unit struggles to keep up with new tools or increased workloads, upgrading to a larger or more efficient compressor will improve operations and save you time.
Outdated Technology
Advances in air compressor technology have made newer models more energy-efficient, quieter, and easier to maintain. If your equipment lacks modern features like variable speed control or efficient cooling systems, investing in a replacement could lower your energy bills and improve performance.
The Impact of Neglected Air Compressor Maintenance
Ignoring maintenance might save you time in the short term, but it can lead to serious consequences for your shop. A poorly maintained air compressor doesn’t just affect its performance—it can impact your entire business.
Reduced Operational Efficiency
A neglected compressor will struggle to deliver consistent performance. Tools powered by it may work slower or less effectively, slowing down tasks and causing frustration for your team.
Higher Repair Costs
Small issues, like clogged filters or minor leaks, can turn into major problems if not addressed. These bigger repairs are often more expensive and time-consuming, potentially requiring entire system overhauls.
Increased Safety Risks
Faulty air compressors can become dangerous. Overheating, oil leaks, or pressure irregularities increase the risk of accidents, putting your team and shop at risk.
Unplanned Downtime
Breakdowns always seem to happen at the worst time—like during a busy day at the shop. Downtime not only disrupts your workflow but can also lead to delays for your customers, affecting their satisfaction and trust in your business.
Lower Customer Satisfaction
When your tools and equipment aren’t reliable, it shows in the quality of your work. Delays and inconsistent results can make customers look elsewhere, potentially damaging your reputation.
Benefits of Professional Repairs and Maintenance
Keeping your air compressor in top condition is crucial for running a smooth and efficient automotive shop. Professional repairs and maintenance offer several advantages that DIY fixes can’t match.
Ensure Safety and Compliance
Certified technicians follow strict safety standards and manufacturer guidelines. They can identify and address potential hazards, ensuring your air compressor operates safely and meets regulatory requirements.
Improve Equipment Lifespan
Regular professional maintenance prevents wear and tear from escalating into major problems. This helps your air compressor last longer, saving you money on premature replacements.
Enhance Performance
Professionals can fine-tune your equipment for optimal performance. From checking pressure settings to cleaning internal components, they ensure your compressor delivers consistent power for all your tools.
Reduce Downtime
With professional repairs, you can address issues quickly and efficiently. Proactive maintenance prevents unexpected breakdowns, keeping your shop running smoothly without unnecessary interruptions.
Save Money in the Long Run
While professional services may seem like an added expense, they often save you money by avoiding costly repairs, reducing energy consumption, and extending the life of your equipment.
How to Choose the Right Air Compressor for Replacement
If your air compressor is no longer meeting your shop’s needs, replacing it is the next step. Choosing the right model ensures you invest in equipment that improves your efficiency and keeps up with your demands.
Evaluate Your Shop’s Needs
- Air Demand: Calculate the total air volume (measured in CFM) required by all the tools in your shop. Make sure the new compressor can handle peak usage without overloading.
- Shop Size: For smaller shops, a compact compressor might be enough. Larger operations may need an industrial-grade unit.
Consider Energy Efficiency
Modern air compressors come with features like variable speed control and advanced cooling systems. These not only save energy but also reduce operational costs in the long run.
Check for Durability and Reliability
Look for brands known for producing durable and low-maintenance compressors. Read reviews and check warranties to ensure you’re getting a reliable product that can handle daily use.
Match the Compressor Type to Your Applications
- Reciprocating Compressors: Best for small-scale, intermittent use.
- Rotary Screw Compressors: Ideal for shops with continuous, high-demand usage.
- Oil-Free Compressors: Perfect for applications requiring clean air, like painting.
Factor in Noise Levels
If your shop has limited space or is in a noise-sensitive area, consider a compressor designed to operate quietly without sacrificing performance.
Plan for Future Growth
Choose a compressor that can accommodate your shop’s growth. Investing in a slightly larger unit now can save you the hassle of upgrading again in the near future.
Conclusion
Your air compressor plays a vital role in your automotive shop’s success. Ignoring the warning signs of wear and tear can lead to costly downtime, safety risks, and reduced efficiency. By staying proactive with maintenance, addressing repairs promptly, and knowing when it’s time for a replacement, you can keep your shop running smoothly and efficiently.
Investing in the right air compressor is more than just upgrading equipment—it’s about ensuring reliability, improving productivity, and meeting customer expectations. Don’t let a failing compressor hold your business back.
Ready to elevate your shop’s performance? Let L&D Shop Solutions help. From expert air compressor services to professional installations, we provide the solutions you need to keep your shop running at its best. Learn more in our pillar blog or contact us today for advice tailored to your needs.