The Role of Compressed Air Systems in Automotive Assembly Lines
Introduction
In the automotive industry, efficiency and precision are crucial for the assembly process. Compressed air systems play a vital role in automotive assembly lines, providing power and control for various tools and equipment used in production. From powering pneumatic tools to enabling automated processes, compressed air systems are integral to ensuring smooth operations, enhancing productivity, and maintaining quality standards. In this blog, we will explore the significant role of compressed air systems in automotive assembly lines, delving into their applications, benefits, and key considerations for implementation.
Powering Pneumatic Tools
Compressed air is the primary power source for pneumatic tools used in automotive assembly. These tools, including impact wrenches, ratchets, drills, and grinders, rely on compressed air to deliver precise and consistent power for tightening bolts, fastening components, and performing various assembly tasks. The high power-to-weight ratio of pneumatic tools allows for efficient and effortless operation, ensuring faster production cycles and reduced operator fatigue. Compressed air systems provide the necessary pressure and volume to meet the demanding requirements of these tools, contributing to the overall efficiency and effectiveness of automotive assembly.
Enabling Automated Processes
Automation plays a significant role in modern automotive assembly lines, streamlining production and improving accuracy. Compressed air systems are essential for powering and controlling automated processes, such as robotic arms, conveyors, and actuators. Compressed air serves as the energy source that drives the movement and operation of these automated components, allowing for precise positioning, handling of components, and assembly operations. The versatility and controllability of compressed air enable seamless integration of automation in automotive assembly, resulting in increased productivity, consistency, and quality.
Quality Control and Testing
Ensuring the quality and reliability of automotive components is of utmost importance. Compressed air systems play a crucial role in quality control and testing processes within the assembly line. They power various testing equipment, such as leak detectors and pressure gauges, used to assess the integrity and functionality of assembled components. Additionally, compressed air is utilized for cleaning and drying components before installation or final packaging, removing debris, and contaminants that could compromise performance or longevity. By facilitating precise and efficient quality control measures, compressed air systems contribute to maintaining high standards and customer satisfaction.
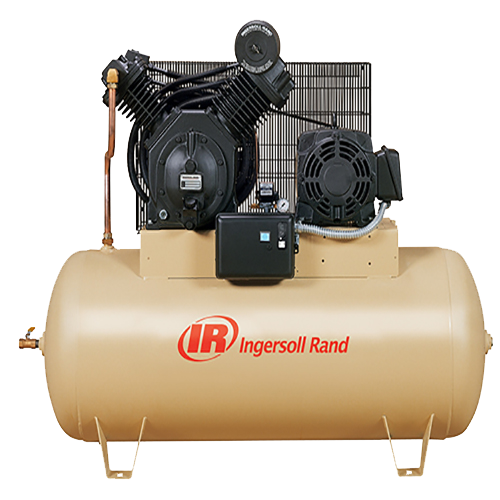
Energy Efficiency and Environmental Considerations
In addition to their functional benefits, compressed air systems offer energy-efficient solutions in automotive assembly. Advanced compressor technologies, such as variable speed drives and energy recovery systems, help optimize energy consumption by adjusting the output to match demand and recovering waste heat for other applications. Implementing energy-efficient compressed air systems not only reduces operating costs but also contributes to environmental sustainability by minimizing energy waste and carbon emissions. Automotive manufacturers are increasingly focused on adopting eco-friendly practices, and compressed air systems offer opportunities to enhance both efficiency and environmental performance.
System Design and Maintenance Considerations
To ensure optimal performance and reliability, proper system design and regular maintenance are essential for compressed air systems in automotive assembly lines. Factors such as air quality, pressure requirements, and pipeline layout must be carefully considered during system design. Maintaining a clean and moisture-free compressed air supply is crucial to prevent damage to pneumatic tools and maintain the integrity of sensitive components. Regular inspections, filter replacements, and preventive maintenance routines help identify and address potential issues before they disrupt production. Engaging experienced professionals in compressed air system installation and maintenance ensures proper system functionality and maximizes the lifespan of the equipment.
Future Innovations and Advancements
The automotive industry is continuously evolving, and so are compressed air systems. Ongoing technological advancements focus on further improving system efficiency, reliability, and control. Innovations like smart compressed air systems, enhanced control algorithms, and predictive maintenance capabilities are emerging, offering manufacturers greater insights into system performance and opportunities for proactive maintenance. Additionally, the integration of Industry 4.0 concepts, such as data analytics and connectivity, allows for real-time monitoring and optimization of compressed air systems. These advancements will drive continuous improvements in automotive assembly processes, resulting in enhanced productivity, quality, and sustainability.
Conclusion
Compressed air systems play a vital role in automotive assembly lines, providing the power, control, and versatility required for efficient and precise production. From powering pneumatic tools to enabling automation, facilitating quality control, and supporting energy-efficient practices, compressed air systems are integral to the success of automotive manufacturing. By understanding the diverse applications and considering important factors such as system design and maintenance, manufacturers can harness the full potential of compressed air systems to optimize productivity, quality, and sustainability in automotive assembly processes.